Software processing outline
This software consists of three blocks, base level processing, TMR0 interruption processing, and TMR1 interruption processing.
On a base level processing, display control of six 7 segments LEDs, reading of three BCD switches, and reading of a UP/DOWN switch are performed.
At the beginning, interruption processing was planed to be used in order to keep the operational stability time of LED device. However, this processing does not require strict time. Therefore, waiting time is made by the subroutine which executes NOP instruction two or more times. Processing is interrupted by interruption processing of TMR0 and TMR1, and time is extended. However, there is no influence in the operation of the equipment.
TMR0 interruption processing is used in order to display change of temperature at intervals of 2 seconds. This is for avoiding that a temperature display changes quickly.
The interruption time obtained by TMR0 is not so long. In the case of 4MHz clock, even if the prescaler is set as 256, the maximum time is 65.5 milliseconds. The TMR0 interruption time in this equipment is 10 milliseconds, and the time for 2 seconds is made by software. Temperature detection and the display are performed in the interval of 2 seconds.
In this processing, reading of TEST mode and temperature comparison processing are performed in addition to reading of temperature sensor and setup of display data. An A/D converter is used for reading of TEST mode and reading of temperature sensor.
TEST mode reading can be performed also on a base level. However, in order to share the 25µs timer subroutine for A/D converter, it is carried out by TMR0 interruption processing.
The temperature comparison conditions for controlling external equipment are shown below. When room temperature is higher than expected temperature, it is in UP mode. When room temperature is lower than expected temperature, it is in DOWN mode. It is somewhat incomprehensible.
 | UP mode | ON condition: | ( Inside > Preset ) and ( Inside > Outside ) |
| OFF condition: | ( Inside =< Preset ) or ( Inside =< Outside ) |
| DOWN mode | ON condition: | Inside < Preset |
| OFF condition: | Inside >= Preset |
TMR1 interruption processing is used in order to obtain comparatively long time to control external equipment. This is to suppress the operation frequency of external equipment.
After turning ON external equipment by the temperature comparison result of TMR0, it may become OFF conditions after 2 seconds by the fall of temperature. In such a case, external equipment will repeat ON/OFF frequently and may get damage. Therefore, if external equipment is turned ON once, it is made to continue operating for several minutes. This time can be changed from 1 minute to 10 minutes with the interval switch.
This equipment can control external equipment in two sets. Please refer to "TMR1 interruption processing" about the control conditions of external equipment.
The use of memories (GPR)
The use of General Purpose Registers are shown below.
out10 | : | BCD data for 10th of Outside |  | seg_ha | : | Head address of Segment pattern |
out1 | : | BCD data for 1st of Outside |
| seg0 | : | "0" display pattern |
in10 | : | BCD data for 10th of Inside |
| seg1 | : | "1" display pattern |
in1 | : | BCD data for 1st of Inside |
| seg2 | : | "2" display pattern |
preset10 | : | BCD data for 10th of Preset |
| seg3 | : | "3" display pattern |
preset1 | : | BCD data for 1st of Preset |
| seg4 | : | "4" display pattern |
out_temp1 | : | Binary data of Outside( 0.25°C ) |
| seg5 | : | "5" display pattern |
in_temp1 | : | Binary data of Inside( 0.25°C ) |
| seg6 | : | "6" display pattern |
out_temp2 | : | Binary data of Outside( 1°C ) |
| seg7 | : | "7" display pattern |
in_temp2 | : | Binary data of Inside( 1°C ) |
| seg8 | : | "8" display pattern |
preset2 | : | Binary data of Preset( 1°C ) |
| seg9 | : | "9" display pattern |
interval | : | BCD data for Interval timer |
| sega | : | Display off pattern |
mode | : | UP/DOWN mode ( 1:up/0:down ) |
| w_save | : | W register save area |
test_mode | : | TEST mode ( 2:OFF/1:IN/0:OUT ) |
| s_save | : | STATUS register save area |
scan_cont | : | Device scan counter |
| temp_check | : | 2 seconds counter |
rc_cont | : |
Input parameter for led_on subroutine
RC port control data |
| presetb | : |
Binary conversion counter
For Preset |
rb_data | : |
Input parameter for led_on subroutine
RB port data |
| presetw | : |
Binary conversion counter
For Preset |
t25us_cnt | : | Counter for 25µs subroutine |
| cont_flag | : | External device control flag |
t200us_cnt | : | Counter for 200µs subroutine |
| repeat | : | Counter for reading check |
t1ms_cnt | : | Counter for 1ms subroutine |
| presetlk | : | Preset last look |
|
|
|
| interval_h | : | Interval counter ( Higher ) |
|
|
|
| interval_l | : | Interval counter ( Low ) |
Initialization processing
The following processings are performed in initialization processing.
 | Port initialization | : | I/O mode of Port A, B, and C is set up. |
| TMR0 initialization | : | Prescaler is set to 64 and interruption is set up for 10ms. |
| TMR1 initialization | : | Prescaler is set to 8 and interruption is set up for 500ms. |
| A/D initialization | : | A/D mode of each port is set up. |
| LED pattern setup | : |
Display pattern of 7 segment LED is set up.
In LED control, '1' is always set to RB7. |
| Work area initialization | : | The value of various work memories is initialized. |
| Interruption setup | : | TMR0 interruption, Peripheral interruption (TMR1), and Global interruption are set up. |
LED and switch scan processing
This processing is processing of a base level. When interruption processing is not performed, it always performs. LED lighting processing and switch reading processing are performed in order.
Process | The contents of execution | Ex time |
1 |
Lighting control of 10th of Outside LED is executed.
Device specification of LED is stored in "rc_cont", display data is stored in "rb_data", and LED lighting control subroutine "led_on" is called. | 1.22ms |
2 | Lighting control of 1st of Outside LED is executed. | 1.22ms |
3 | Lighting control of 10th of Inside LED is executed. | 1.22ms |
4 | Lighting control of 1st of Inside LED is executed. | 1.22ms |
5 | Lighting control of 10th of Preset LED is executed. | 1.22ms |
6 | Lighting control of 1st of Preset LED is executed. | 1.22ms |
7 |
Reading of 10th of Preset switch is executed.
LED is turned off in order to prevent the malfunction by PORTB data at the time of a device change. It may be unnecessary.
RB0 to RB6 is changed to input mode.
The change waiting time of a device is 200 milliseconds. Even if shorter, I think it is satisfactory.
On account of the circuit, as for the read BCD data, 0 and 1 are reverse. It is made reversed by "xorlw" instruction. 4 bits (BCD) of low ranks are stored. | 0.21ms |
8 |
Reading of 1st of Preset switch is executed.
Data is read 200 milliseconds later after switching a device. It is changed into binary data using the value of the 10th read by process 7.
A changed value is temporarily saved in "presetlk". The value of Preset is judged effective when the same value is continuously read three times. After the confirmation, the value is saved in "preset2".
This is because to be abnormal occurred to the reading value by the performance test. Refer to "Troubleshooting" | 0.33ms |
9 |
Reading of an interval switch and reading of a UP/DOWN switch are executed.
Only when reading an interval switch, RB7 is set as '0'. Data is read 200 milliseconds later. Because the timer value is equal to or more than 1, when the data is '0', it is converted into 10.
RB0 to RB6 is changed to output mode.
Finally a UP/DOWN switch is read and data is set into "mode" according to the state of the switch. ( 1:up/0:down ) | 0.22ms |
led_on subroutine
355
356
357
358
359
360
361
362
363
364
365
366
367
368
369
370 | ;--------------------------------------------------------
; LED ON subroutine
;--------------------------------------------------------
led_on
movlw b'11111111'
movwf portb ;LED OFF
movfw rc_cont ;Read RC control data
movwf portc ;Set PORTC
call t200us ;Wait 200 microseconds
movfw rb_data ;Read disp digit
addwf seg_ha,w ;HA + Digit
movwf fsr ;Set address
movfw indf ;Read 7seg data
movwf portb ;Set PORTB
call t1ms ;Wait 1 millisecond
return |
LED is turned OFF first. This is for preventing displaying previous data on the following LED, when a device is changed.
Changing by the device is done by the data of "rc_cont" and the setting of display data is done 200 milliseconds later.
An LED display pattern is picked out from the pattern table stored in the work area. The binary data of a display number is added to the head address of a table, and the pattern data in the address is read. This is indirect address processing. After outputting pattern data to PORTB, it waits for 1 millisecond. This is for making the continuation lighting time of one LED. Flickering of a display can be prevented by making LED continuation lighting time longer than the reading time of a switch. It may be satisfactory even if shorter. The display state when changing time is not checked. |
The above-mentioned execution time is a reference value. Since a BCD conversion process step changes with the value of reading data, some processing time changes. By the simulator, the time of one cycle was about 8.33ms. This is the value which set up a break point at the head of process 1 and measured.
Interruption processing
396
397
398
399
400
401
402
403
404
405
406
407
408
409
410
411
412
413
414
415
416
417 | ;********************************************************
; Interruption Process
;********************************************************
int
movwf w_save ;Save W register
movfw status ;Read STATUS reg
movwf s_save ;Save STATUS reg
bcf status,rp0 ;Change to Bank0
btfsc intcon,t0if ;Check TMR0
goto temp_detect ;TMR0 time-out
btfsc pir1,tmr1if ;Check TMR1IF
goto out_control ;TMR1 time-out
;********************************************************
; END of Interruption Process
;********************************************************
int_end
movfw s_save ;Read saved STATUS reg
movwf status ;Recover STATUS reg
swapf w_save,f ;Read saved W register
swapf w_save,w ;Recover W register
retfie |
If TMR0 or TMR1 carry out a timeout, an interrupt will occur. It is not known at which time of base level processing interruption processing occurs. If the contents of the register currently used on the base level are rewritten by interruption processing, processing of a base level cannot be continued. Therefore, before beginning interruption processing, it is necessary to save the contents of the registers shared with base level. These registers are resaved to the original contents, when interruption processing is completed. The contents of W register and the STATUS register are saved in this processing.
In the saving process, the important thing is not to change the contents of the STATUS register. The various flags of a processing result are stored in the STATUS register. The example by "btfss" instruction is shown below.
Base level process | Interruption process | Explanation |
movfw xyz | | ;Read xyz for the process judgement |
| Interruption generating | ;Execute from address 0004 |
| goto int
:
int
movwf w_save
movfw status
movwf s_save
:
:
:
int_end
movfw s_save
movwf status
swapf w_save,f
swapf w_save,w
retfie | ;
;
;
;
;STATUS reg contents before movfw exec
;STATUS reg contents by the base level
;
;W and STATUS reg can be used
;
;
;
;
;STATUS reg contents by the base level
;swapf doesn't change STATUS reg
;
; |
| Interruption end | ;Execute before interrupt |
btfss status,z | | ;STATUS is based on "movfw xyz" |
The "movfw"( directive of movf ) directive is used when a STATUS register is saved. If this directive is used, the flag of a STATUS register will change. However, the timing from which a flag changes is after executing a command. Therefore, the contents before executing "movfw" are stored in the W register. It is the contents executed on the base level.
The "swapf" instruction is used when restoring W register. If the contents of the W register are restored by "movf" instruction, the flag of the STATUS register will change. Therefore, W register is restored by the "swapf" instruction which does not affect a flag.
In this interruption process, after save of the registers are completed, a judgment of interruption type is made. It is the judgement of TMR0 or TMR1. Each processing is executed by the interruption type.
TMR0 interruption processing
419
420
421
422
423
424
425
426
427
428
429 | ;%%%%%%%%%%%%%%%%%%%%%%%%%%%%%%%%%%%%%%%%%%%%%%%%%%%%%%%%
; Temperature detection Process (10ms)
;%%%%%%%%%%%%%%%%%%%%%%%%%%%%%%%%%%%%%%%%%%%%%%%%%%%%%%%%
temp_detect
bcf intcon,t0if ;Clear T0IF
movlw 100 ;Set Time value
movwf tmr0 ;Write TMR0 register
decfsz temp_check,f ;count - 1
goto int_end
movlw 200
movwf temp_check ;Set 2 seconds |
The "t0if" interruption flag of "intcon" register is cleared first. If this flag is not cleared, an interruption state will continue and if "retfie" instruction is executed when interruption processing is ended, although it is not in a timeout state, either, TMR0 interrupt will occur.
Next, TMR0 value is set up. TMR0 counts up a value, and when a counter overflows, an interrupt generates it. Therefore, when an interrupt occurs, the value of TMR0 is "0."In order to generate the next interruption after the time of a schedule, the value of TMR0 is set up again.
This time, interruption of TMR0 is set as 10 milliseconds. The process to execute by TMR0 interruption is every 2 seconds. Therefore, 10 milliseconds is counted 200 times with the counter (temp_check) of software, and 2 seconds is made. In fact, 200 is set to "temp_check" and the method of subtracting is taken. This is because a count-out judgment can be made simultaneously with subtraction and the process can be simplified, if "decfsz" instruction is used. In interruption in 2 seconds, interruption processing is ended only by subtracting a counter.
TEST mode check processing
431
432
433
434
435
436
437
438
439
440
441
442
443
444
445
446
447
448
449
450
451
452
453
454
455
456 | ;------------------ TEST mode check ---------------------
mode1
movlw b'01011001' ;ADCS=01 CHS=AN3 ADON=ON
movwf adcon0 ;Set ADCON0 register
call t25us ;Wait 25 microseconds
bsf adcon0,2 ;Start A/D conversion
mode2
btfsc adcon0,2 ;Conversion end ?
goto mode2 ;No.
movlw 168 ;Set 3.3V
subwf adresh,w ;AN3 - 3.3V
btfss status,c ;AN3 >= 3.3V
goto mode3 ;No.
movlw 2 ;Yes.
movwf test_mode ;Set TEST OFF
goto temp0
mode3
movlw 87 ;Set 1.7V
subwf adresh,w ;AN3 - 1.7V
btfss status,c ;AN3 >= 1.7V
goto mode4 ;No.
movlw 1 ;Yes.
movwf test_mode ;Set IN TEST
goto temp0
mode4
clrf test_mode ;Set OUT TEST |
The output of a temperature sensor is amplified by the OP amplifier and digital conversion is carried out by an A/D converter. Usually, a temperature display is displayed in °C unit. However, the more detailed temperature display is convenient for gain adjustment of an OP amplifier. As for an A/D converter, 10-bit digital output is obtained. 6 bits of higher ranks of them are made to correspond to °C with this equipment. Therefore, if the 4 bits of the remaining low ranks are used, 1/16°C(0.0625°C) information can be acquired. If it uses to Preset, the display of 4 figures below decimal point is possible. However, with this equipment, the display of 0.25°C unit is realized using 2 bits of higher ranks of the 4 bits.
The information of TEST mode is taken in by an A/D converter. +5V is as TEST OFF, +2.5V is as IN TEST and 0V is as OUT TEST.
The judgment in the mode is performed with the value which divided 5V into three equally. 0V to +1.7V is as OUT TEST, over +1.7V to 3.3V is as IN TEST and Over +3.3V is as TEST OFF.
The information of TEST mode, Outdoor temperature sensor and Indoor temperature sensor is converted in the digital in the order by A/D converter. With the specification of A/D converter, it is required to make time until it takes analog information into PIC after changing an input port. In the case of a 4MHz clock, time of necessity is (1/4)*8 = 2µs in 1-bit conversion. In the case of PIC16F873, the output is 10 bits. However, every 1 bit processing time is added forward and backward, and the time for 12 bits is required. Therefore, after changing a port before starting an A/D converter, it is necessary to make the waiting time of 12b x 2us/b = 24µs. The waiting time in this subroutine is 25µs. The A/D converter is started after passing for 25µs. Completion of A/D conversion supervises and checks after starting that the "GO/DONE" bit of "adcon0" register is set to "0."
8 bits of higher ranks of the output of an A/D converter are the value which divided 5V into 255. It is about 0.0196V. So, +1.7V is 1.7/0.0196 = 87 and +3.3V is 3.3/0.0196 = 168.
Temperature data reading processing
458
459
460
461
462
463
464
465
466
467
468
469
470
471
472
473
474 | ;------------ OUT-SIDE temperature detection ------------
temp0
movlw b'01001001' ;ADCS=01 CHS=AN1 ADON=ON
movwf adcon0 ;Set ADCON0 register
call t25us ;Wait 25 microseconds
bsf adcon0,2 ;Start A/D conversion
temp1
btfsc adcon0,2 ;Conversion end ?
goto temp1 ;No.
movfw adresh ;Read result
addlw 8 ;Add 2deg-c
movwf out_temp1 ;Save (unit:0.25deg-c)
movwf out_temp2 ;Set data
rrf out_temp2,f ;Rotate Right
rrf out_temp2,f ;Rotate Right
movlw b'00111111' ;Set mask
andwf out_temp2,f ;Save (unit:1deg-c) |
Digital conversion of the information on a temperature sensor is carried out by an A/D converter. With this equipment, 8 bits of higher ranks of the converted value are used. 1 bit is made equivalent to 0.25°C. 6 bits of higher ranks correspond to 1°C.
The output of a temperature sensor is 0V at 2°C. Therefore, it is necessary to add 2°C to a conversion result. Since 1 bit is 0.25°C, 8 is added to adding 2°C.
Temperature display processing
Three kinds of displays can be performed by TEST mode. Usually, outdoor temperature and indoor temperature are displayed per 1°C in the state of TEST OFF.
 |
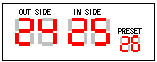
TEST OFF |
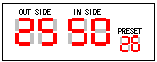
IN TEST |
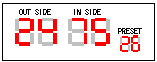
OUT TEST |
When indoor temperature is 25.50°C and outdoor temperature is 24.75°C, a display becomes as it is shown in the above figure by TEST mode.
Since the data obtained by an A/D converter is binary, it is necessary to separate the 10th place and the 1st place. The number of times which subtracted 10 from binary data is the 10th place, and remainder is the value of the 1st place. The end of conversion is judged because the subtraction result became negative. Therefore, when it becomes negative, 10 is added and it is made normal remainder value.
552
553
554
555
556
557
558
559
560
561
562
563
564
565
566
567
568
569
570
571
572
573
574
575
576
577
578
579
580
581 | temp43
btfss in_temp1,1 ;1X ?
goto temp45 ;No. 0X
btfss in_temp1,0 ;11 ?
goto temp44 ;No. 10
movlw 7 ;Set .75 deg
movwf in10
movlw 5
movwf in1
goto comp0 ;Jump to comparison
temp44
movlw 5 ;Set .50 deg
movwf in10
movlw 0
movwf in1
goto comp0 ;Jump to comparison
temp45
btfss in_temp1,0 ;01 ?
goto temp46 ;No. 00
movlw 2 ;Set .25 deg
movwf in10
movlw 5
movwf in1
goto comp0 ;Jump to comparison
temp46
movlw 0 ;Set .00 deg
movwf in10
movlw 0
movwf in1
goto comp0 ;Jump to comparison |
In IN TEST mode and OUT TEST mode, the value of 1°C unit is displayed on an outdoor display part, and the value below a decimal point is displayed on the indoor display part. 2 bits of low ranks of 8-bit binary data are used for the display below a decimal point. The number of states is four. 00 = 0.00°C, 01 = 0.25°C, 10 = 0.50°C, 11 = 0.75°C. Since the number of states is four, a state is judged and the indicated value is written in the area for an indoor display.
Temperature comparison processing
629
630
631
632
633
634
635
636
637
638
639
640
641
642
643
644
645
646
647
648
649
650
651
652
653
654
655
656
657 | ;---------- Temperature comparison processing -----------
comp0
movfw mode ;Read mode(1:up 0:down)
btfsc status,z ;Up ?
goto comp2 ;Jump to down mode
;***(Up mode)
movfw in_temp2 ;Read in-side
subwf preset2,w ;preset - in-side
btfsc status,c ;preset >= in-side ?
goto comp1 ;(>=)
movfw in_temp2 ;(<)Read in-side
subwf out_temp2,w ;out-side - in-side
btfsc status,c ;out-side >= in-side ?
goto comp1 ;(>=)
bsf cont_flag,flag ;(<)Set control flag
goto int_end ;Jump to int end
comp1
bcf cont_flag,flag ;Clear control flag
goto int_end ;Jump to int end
;***(Down mode)
comp2
movfw preset2 ;Read preset
subwf in_temp2,w ;in-side - preset
btfsc status,c ;in-side >= preset ?
goto comp1 ;(>=)
bsf cont_flag,flag ;(<)Set control flag
goto int_end ;Jump to int end |
This is important processing of this equipment. But processing is simple. First, UP/DOWN mode is checked and it jumps to each processing.
UP mode : The mode which controls external equipment when indoor temperature is higher than preset temperature.
An indoor temperature and a preset temperature are compared first. When the indoor temperature is higher than preset temperature, it corresponds to the conditions which control external equipment. Indoor temperature and outdoor temperature are compared before that. External equipment is not operated when outdoor temperature is higher than indoor temperature. When the outdoor temperature is lower, it becomes the control conditions of external equipment. If it becomes the conditions which control external equipment, "1" will be set as the "flag" bit of "cont_flag". If this bit is set to "1", processing of TMR1 will operate external equipment.
DOWN mode : The mode which controls external equipment when indoor temperature is lower than preset temperature.
Only indoor temperature and preset temperature are compared. When the indoor temperature is lower than preset temperature, it becomes the control conditions of external equipment, and "1" is set as the "flag" bit of "cont_flag".
TMR1 interruption processing
671
672
673
674
675
676
677
678
679
680
681
682
683
684
685
686
687
688
689
690
691
692
693
694
695
696
697
698
699
700
701
702
703
704
705
706
707
708
709
710
711
712
713
714
715
716
717
718
719
720
721 | ;%%%%%%%%%%%%%%%%%%%%%%%%%%%%%%%%%%%%%%%%%%%%%%%%%%%%%%%%
; Output control Process (500ms)
;%%%%%%%%%%%%%%%%%%%%%%%%%%%%%%%%%%%%%%%%%%%%%%%%%%%%%%%%
out_control
bcf pir1,tmr1if ;Clear TMR1IF
movlw h'0b' ;
movwf tmr1h ;Set TMR1H register
movlw h'dc' ;
movwf tmr1l ;Set TMR1L register
movfw cont_flag ;Read all control flags
btfsc status,z ;All flags OFF ?
goto int_end ;Yes. Jump to int end
btfsc cont_flag,o1 ;OUT1 control flag ON ?
goto cont1 ;Yes.
btfsc cont_flag,o2 ;OUT2 control flag ON ?
goto cont1 ;Yes.
;***(1st control)
bsf cont_flag,o1 ;Set OUT1 control flag
bsf porta,o1 ;OUT1 ON
call time_set ;Set timer value
goto int_end ;Jump to int end
cont1
decfsz interval_l,f ;time -1
goto int_end ;Not time-out
movlw 1
subwf interval_h,f ;Higher value check
btfss status,c ;Value >= 1 ?
goto cont2 ;Value = 0 (Time-out)
movlw h'ff'
movwf interval_l ;Set Lower value
goto int_end ;Not time-out
cont2
btfss cont_flag,flag ;Control flag ON ?
goto cont3 ;No.
bsf cont_flag,o2 ;Set output2 flag
bsf porta,o2 ;OUT2 ON
call time_set ;Set timer value
goto int_end ;Jump to int end
cont3
btfss cont_flag,o2 ;Output2 flag ON ?
goto cont4 ;No.
bcf cont_flag,o2 ;Clear output2 flag
bcf porta,o2 ;OUT2 OFF
call time_set ;Set timer value
goto int_end ;Jump to int end
cont4
bcf cont_flag,o1 ;Clear output1 flag
bcf porta,o1 ;OUT1 OFF
goto int_end ;Jump to int end |
The "tmr1if" interruption flag of "pir1" register is cleared first. TMR1 is counted by 16 bits with two counters, "tmr1h" and "tmr1l". The value of prescaler is a maximum of 8. Therefore, with a 4MHz clock, it is countable to 1us x 8 x 65536 = 524,288us. In this time, the initial value of the counter is set to 3036, and interruption is generated in 62,500counts x 8us = 500 milliseconds.
The "flag" bit of "cont_flag" is checked in every 500 milliseconds. Therefore, the external device control demand performed by temperature comparison processing is detected by processing of TMR1 after 500 milliseconds at the latest. The drive situation of external equipment is managed by "o1" bit and "o2" bit of "cont_flag". A management bit is discontinuous. o1 is the 2nd bit and o2 is the 5th bit. This is because the circuit 1 port for external equipment is RA2 and circuit 2 port is RA5. A label called o1 and o2 is shared with bit specification of PORTA.
When both of bits are "0", the external circuit is in the state which is not driven. In this state, the circuit 1 will be driven if the flag bit of cont_flag is set to "1". "o1" bit of "cont_flag" is set to "1" and RA2 of PORTA is turned ON. Thereby, relay 1 drives and external equipment 1 begins to operate. An interval timer is set up after it. An interval timer is a timer which manages the time when external equipment is operating. A preset value is changed with the value of an interval switch.
When "1" is detected for "o1" or "o2" with the check in a cycle of 500 milliseconds, subtraction of an interval timer is performed. Driving external equipment is continued until an interval timer carries out a timeout, even if the "flag" bit of "cont_flag" is set to "0", before an interval timer carries out a timeout.
Please refer to the following table for the external equipment drive conditions in each state.
 | flag | o1 | o2 | Control state |
| 0 | 0 | 0 | Nothing is driven. |
| 1 | 0 -> 1 | 0 | External equipment 1 is driven. |
| 1 | 1 | 0 -> 1 | External equipment 1 and 2 is driven. |
| 1 | 1 | 1 | External equipment is continuation-driven. |
| 0 | 1 | 1 -> 0 | External equipment 2 is stopped. |
| 0 | 1 -> 0 | 0 | External equipment 1 is stopped. |
| X | 0 | 1 | This condition does not happen. |
|